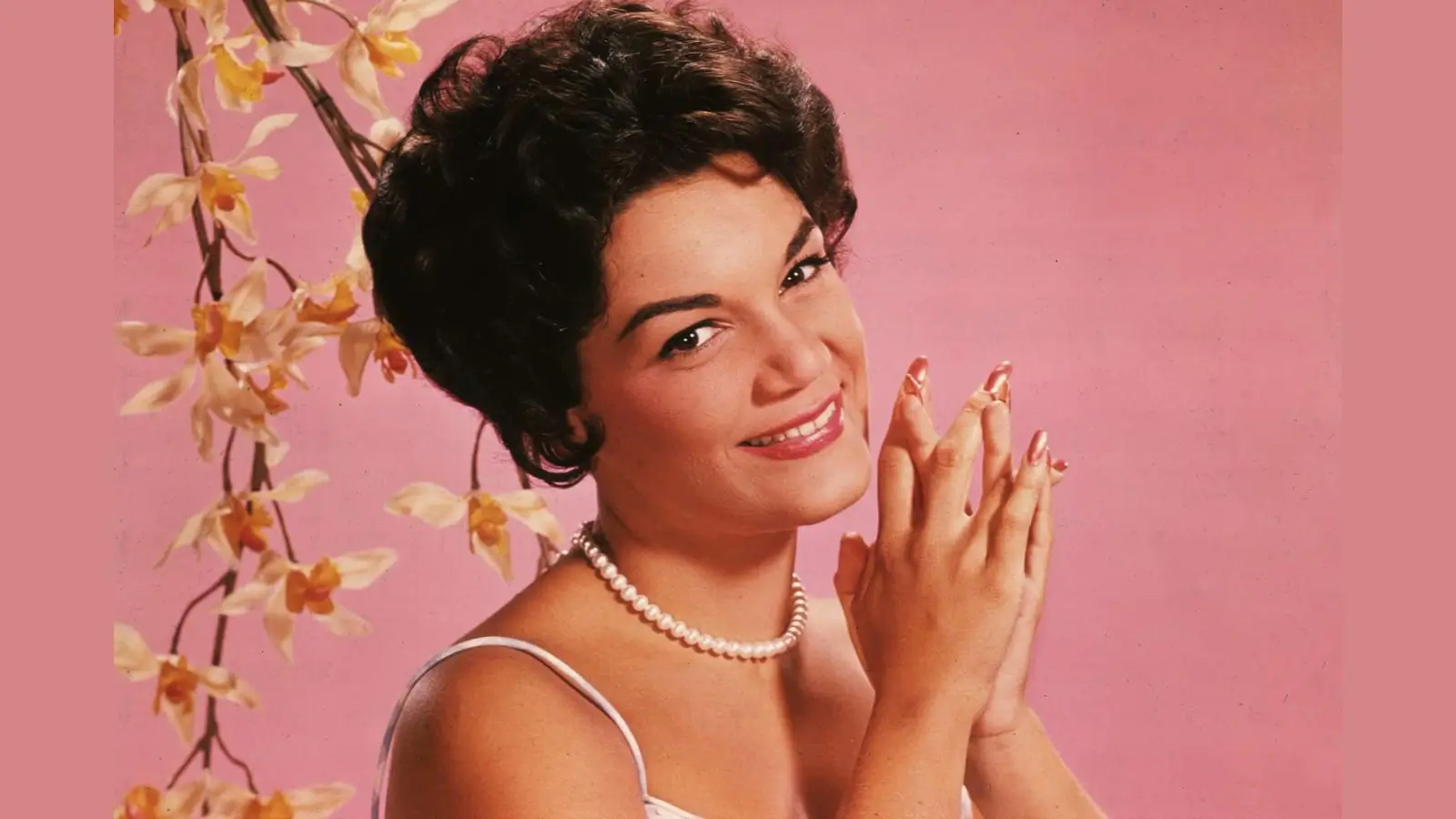

With around 100 fatalities and 35,000 injuries each year in the US from forklift incidents, and thousands in the UK, it has become apparent that the current passive approach to safety is simply inadequate. Although difficult to quantify, a huge portion of these incidents are preventable through better controls, particularly within an optimized visual safety system.
The issue with signage is often that it’s there to tick the boxes of regulation rather than to be used on the front foot. Signage is a powerful way to influence behavior and it forms the foundation of robust warehouse safety protocols. Well-designed signage is about being a clear and universally understood language that helps control high-consequence environments. For signage solutions ideas and purchases, Seton offers a variety of regulated options. Check it out, along with this article on signage strategy and protection for external accidents.
Adherence to OSHA and ISO signage standards is always going to be the baseline for accident risk mitigation. OSHA mandates a safe work environment and defers to ANSI standards, specifically ANSI Z535, for the specs on visual safety communication.
This family of standards provides a unified system for hazard recognition, helping bring standardization to the workplace. It dictates the use of words like "Danger" for imminent hazards that will cause death or injury, "Warning" for hazards that could, and "Caution" for those that may cause minor injuries. These hierarchies are important to avoid building a tolerance for hazard signs which could lead to them being ignored.
To achieve universal comprehension though, they must use ISO 7010 graphical symbols. These transcend language barriers, which are often prevalent in warehouses which attracts a lot of immigrant workers.
The long-term efficacy of forklift warning signage is all about its material composition and construction. The message is important, but it may fade over time. Material selection should align with the specific environment it’ll be placed in to ensure long-term visibility and durability.
So, for outdoor loading docks or areas exposed to the elements, signs made from reflective aluminum can provide better visibility in low light and withstand harsh weather. Photoluminescent signs are important for indoor placement as they absorb ambient light and remain visible during power failures. Floor signs require aggressive, high-tack adhesives to resist peeling and abrasion from the constant traffic. Signs in high-impact zones may need rigid, shatter-resistant substrates.
So, choosing the right material is mostly a technical decision that prolongs both the lifespan and visibility.
Optimal sign placement visibility is all about maximizing the reaction of the sign on workers. OSHA guidelines and research shows that signs should be placed in the immediate vicinity of a hazard - not too early, but not to late (in terms of the movement towards the hazard).
In a dynamic warehouse, this isn’t actually easy. Primary signage is what’s used as warnings for blind corners and major intersections and should be posted at a height visible to both forklift operators and pedestrians. This is often between 5 and 7 feet from the floor, but it can depend.
This is often supplemented by floor markings that delineate pedestrian-only walkways and forklift traffic lanes (as per OSHA standard 1910.176). For high-risk areas like blind intersections where static signs may not be sufficient, modern solutions like radar-activated projected signage can alert pedestrians to approaching traffic, as proven effective in examples like West Linn Paper Company.
One investigative report showed that the absence of clearly segregated pedestrian walkways from forklift ones contributed to a severe injury. It’s become clear with more and more reporting that inadequate visual separation between personnel and forklift traffic is one cause of high incident rates.
Similarly, the previously mentioned West Linn Paper Company dramatically reduced concerns about forklift speeding issues after they installed their radar-activated speed signs near its loading dock. These aren’t too different to the dynamic, real-time speed signs we see driving around that tells us to slow down when it detects high speeds. It shows that signage can be more effective when it can be switched off during dormant or unnecessary times, so its impact is greater once lit.
To translate strategy into action, safety managers should develop an implementation checklist to follow as a clear framework that can be replicated in the future. Here is a starting point for a five-step process: