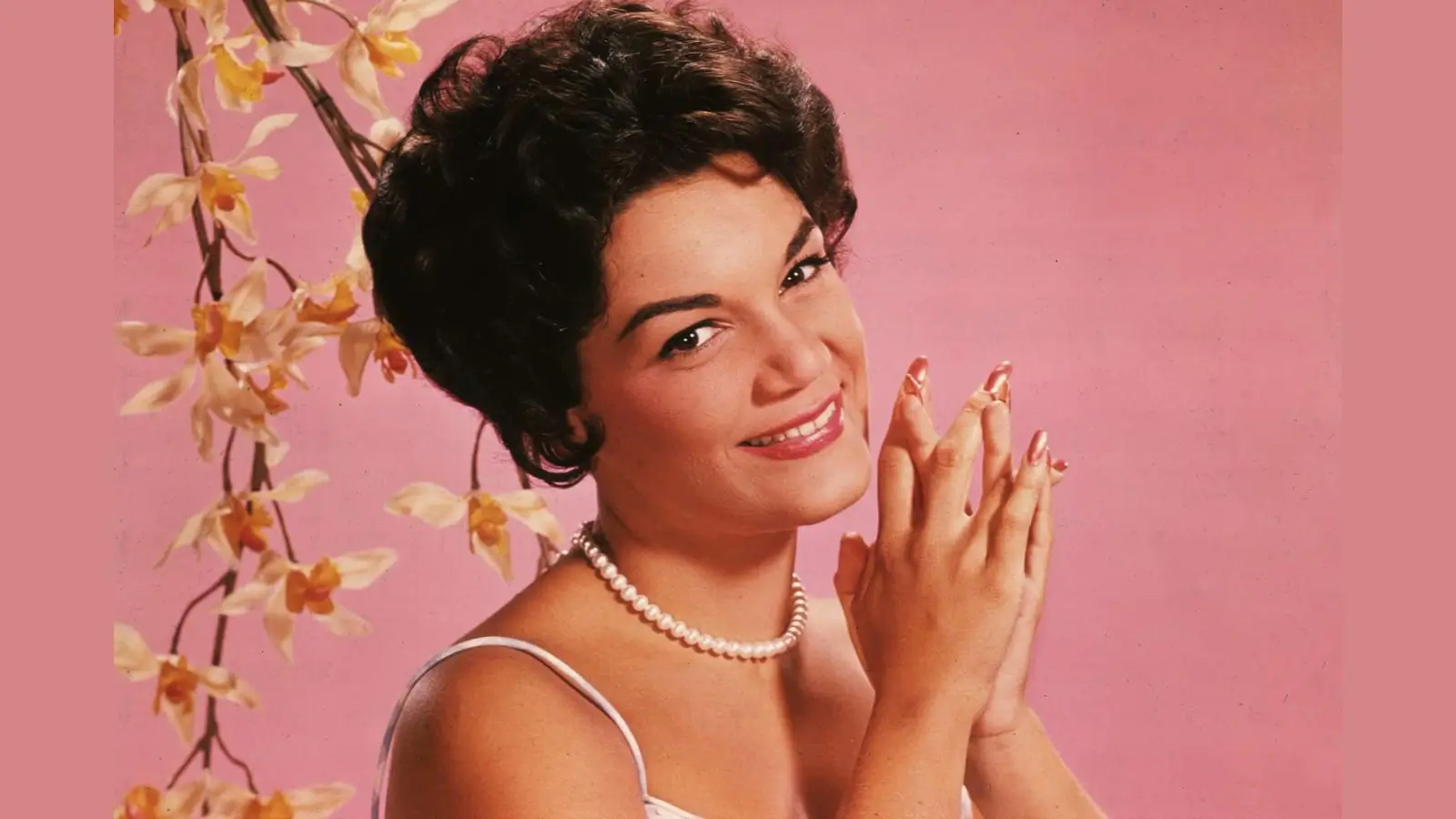

Diaphragm pumps shine when it comes to handling all sorts of fluids. Their design makes them super adaptable. They can deal with stuff that other pumps just can't.
They're a solid choice if you need something that can switch between different materials without a fuss. This is a big deal in industries where the fluid type changes often.
Diaphragm pumps are built to be flexible. They can be adjusted to work with different flow rates and pressures, making them useful in many situations.
Diaphragm pumps don't care if the material is thick or gritty. They just keep on pumping. This is because of how they're designed.
The diaphragm creates a seal that keeps the moving parts away from the fluid. This prevents wear and tear from abrasive materials.
They are great for moving slurries, paints, and other tough-to-handle substances. This makes them a go-to choice for many industries.
Diaphragm pumps can be made from materials that resist corrosion. This means they can handle strong chemicals without breaking down.
Different materials like Teflon or stainless steel can be used. The choice depends on the specific chemicals being pumped.
This resistance to chemicals makes diaphragm pumps ideal for chemical processing plants. They can safely move acids, solvents, and other dangerous liquids.
Fluids with lots of solids can be a problem for many pumps. Diaphragm pumps, however, are built for this.
Their design allows them to move fluids with a high percentage of solid particles. This is important in wastewater treatment and mining.
The large internal passages prevent clogging. This ensures continuous operation even with challenging fluids. Diaphragm pumps are a great choice for these applications.
Diaphragm pumps are built with safety in mind. They offer features that reduce risks in tough work areas. This makes them a good choice where safety is key.
They are designed to prevent accidents. Diaphragm pumps can handle dangerous materials safely.
These pumps help keep workers safe. They also protect the environment.
Diaphragm pumps shine in explosive settings. They often use air instead of electricity, cutting down the risk of sparks. This is super important where there are flammable gases or liquids.
Because they don't use electricity, there's less chance of an explosion. This makes the workplace much safer.
They are a safe bet for industries like chemical processing and oil and gas.
Handling flammable liquids needs extra care. Diaphragm pumps are designed to avoid sparks. This is a big deal when moving things like gasoline or solvents.
Diaphragm pumps can be made with special materials. These materials don't create static electricity, which can cause sparks.
Using diaphragm pumps reduces the chance of fires. This helps protect people and property.
Many industries have strict safety rules. Diaphragm pumps can be made to meet these rules. This includes using materials that are safe for food or chemicals.
Some pumps are made for specific jobs. For example, there are pumps for handling food and pumps for dealing with strong chemicals.
Here's a quick look at some safety features:
Diaphragm pumps are built to last. Their design focuses on robustness, meaning they can handle tough conditions without breaking down. This is a big plus when you need equipment that won't quit on you.
They also don't need a ton of upkeep. Fewer moving parts equals less that can go wrong. That saves time and money in the long run.
This makes them a smart choice for industries where reliability is key.
Diaphragm pumps are made for the grind. They can take a beating from dust, debris, and even some corrosive materials. This is because they're often built with heavy-duty materials that can withstand harsh environments.
Their simple design contributes to their toughness. Fewer complicated parts mean less chance of something failing when the going gets tough. This is especially important in places where conditions are unpredictable.
Think of a construction site or a mine. These are places where equipment needs to be able to handle a lot, and diaphragm pumps are up to the task.
It's all about the materials. Diaphragm pumps use things like Teflon, elastomers, and specialized alloys. These materials resist wear and tear, extending the pump's lifespan.
Choosing the right material is key. It depends on what you're pumping. Corrosive chemicals need different materials than abrasive slurries. Getting it right means the pump lasts longer and performs better.
The right materials make all the difference in the world.
Downtime is a killer. When equipment breaks down, it costs money and time. Diaphragm pumps help avoid this because they're reliable and easy to fix.
Their simple design means repairs are often quick and easy. You don't need a specialized technician to get them back up and running. This is a huge advantage in remote locations or when time is of the essence.
Less downtime means more productivity. In industries like chemical processing or wastewater treatment, every minute counts. Diaphragm pumps help keep things moving.
Diaphragm pumps shine when it comes to self-priming. They can start pumping without needing to be filled with fluid first. This is super useful when the fluid supply isn't constant.
They can also run dry for short periods without damage. This makes them a reliable choice in tough spots.
This capability is a game-changer in environments where other pumps might fail.
Diaphragm pumps can deliver a more consistent flow. This is important for applications where a steady stream is needed.
They minimize the pulsations that can occur with other types of pumps. This leads to more reliable and predictable results.
Here's a quick look at why this matters:
Diaphragm pumps are great for precise control. They can accurately dose and inject fluids. This is key in chemical processing and other industries.
The adjustable flow rates allow for fine-tuning. This ensures the right amount of fluid is delivered every time.
Consider these applications:
Diaphragm pumps offer operational advantages that make them a solid choice for many applications.
Diaphragm pumps might seem pricier initially. However, their robustness and efficiency often lead to lower total ownership costs over time. It's about weighing that initial investment against the long-term benefits. Think of it like buying a well-built car; it costs more at first, but you save on repairs down the road.
Consider the energy efficiency and maintenance needs. These factors significantly impact the overall cost of running the pump. A little extra spent upfront can save a lot later.
Choosing the right diaphragm pump means looking beyond the sticker price. It's about finding the best value for your specific needs.
Modern diaphragm pumps are designed for peak efficiency. They minimize air consumption and reduce energy waste. This makes them more cost-effective in the long run.
Improvements in pump performance translate to significant cost savings. Reduced pulsation also minimizes the risk of fluid hammer, which can damage piping systems. This is a key advantage in many industrial settings.
Think about the energy savings over the pump's lifespan. It adds up, making diaphragm pumps a smart choice for many applications.
Diaphragm pumps shine when it comes to maintenance. They need less attention, which is great for critical applications where downtime is costly. This is especially true in places like car washes or chemical plants.
The ease of maintenance and repair is a big plus. This is especially important in remote areas where technical support might be limited. A pump that's easy to fix keeps things running smoothly.
Reduced maintenance translates directly to lower operating expenses. Less downtime means more productivity and a healthier bottom line.
Chemical processing plants deal with some seriously nasty stuff. Diaphragm pumps are built to handle it. They can move acids, solvents, and other hazardous materials without breaking down.
These pumps use materials like PTFE and Hastelloy. These materials resist corrosion, which is super important when you're pumping harsh chemicals. This keeps the pumps running longer and safer.
Diaphragm pumps are a solid choice for chemical plants.
In chemical processing, accuracy is key. You can't just dump chemicals in and hope for the best. You need to measure things out carefully.
Diaphragm pumps offer precise control over flow rates. This makes them ideal for dosing and injection applications. They ensure the right amount of chemical is added every time.
This precision helps maintain product quality and safety. It also reduces waste and saves money.
Chemical plants can be tough on equipment. Temperatures can be high, and chemicals can be aggressive. Pumps need to be able to handle these conditions.
Diaphragm pumps are designed for durability. They can withstand extreme temperatures and pressures. This makes them reliable in demanding environments.
Diaphragm pumps are often used in sterile fluid transfer, where the pump’s ability to operate without generating heat or contamination is critical. The use of high-purity materials, such as PTFE and stainless steel, ensures that these pumps meet the stringent requirements of pharmaceutical manufacturing, providing reliable and consistent performance in even the most demanding environments.
They keep working even when things get rough.
Wastewater treatment plants rely on robust equipment. Diaphragm pumps are crucial for handling various fluids. They offer reliability in demanding conditions.
These pumps play a vital role in maintaining environmental sustainability. They efficiently manage, transfer, and process wastewater. Their design makes them ideal for these applications.
Diaphragm pumps provide a combination of durability and chemical resistance. This makes them essential for wastewater treatment.
Diaphragm pumps excel at handling thick sludge and slurries. These materials are common in wastewater treatment. They ensure efficient transfer without clogging.
These pumps can manage fluids with high solid content. This is essential for primary treatment processes. They contribute to effective waste management.
Diaphragm pumps are designed to handle abrasive materials. This reduces wear and tear, extending the pump's lifespan.
Wastewater treatment plants present harsh conditions. Diaphragm pumps are built to withstand these challenges. They offer reliable performance.
These pumps can operate in corrosive environments. This is due to their chemical-resistant materials. They maintain efficiency even with harsh chemicals.
Diaphragm pumps are designed for continuous operation. This minimizes downtime and ensures consistent performance. They are a dependable choice for wastewater facilities.
Diaphragm pumps are designed to handle fluids with high solid content. This is a key requirement in wastewater treatment. They prevent clogging and maintain flow.
These pumps can manage sludge, slurries, and other solid-laden materials. This ensures efficient processing of wastewater. They contribute to effective waste removal.
Diaphragm pumps offer consistent performance even with varying fluid densities. This makes them a versatile solution for wastewater applications.
So, when you look at it, diaphragm pumps are pretty important for tough jobs. They can handle all sorts of liquids, even the nasty ones, and they keep working even when things get rough. This makes them a good choice for places like chemical plants or wastewater treatment centers. They're built to last, and they don't need a ton of upkeep, which is a big plus. Picking the right one means thinking about what you're pumping and where it's going to be used. But overall, these pumps are a solid bet for keeping things moving in challenging spots.