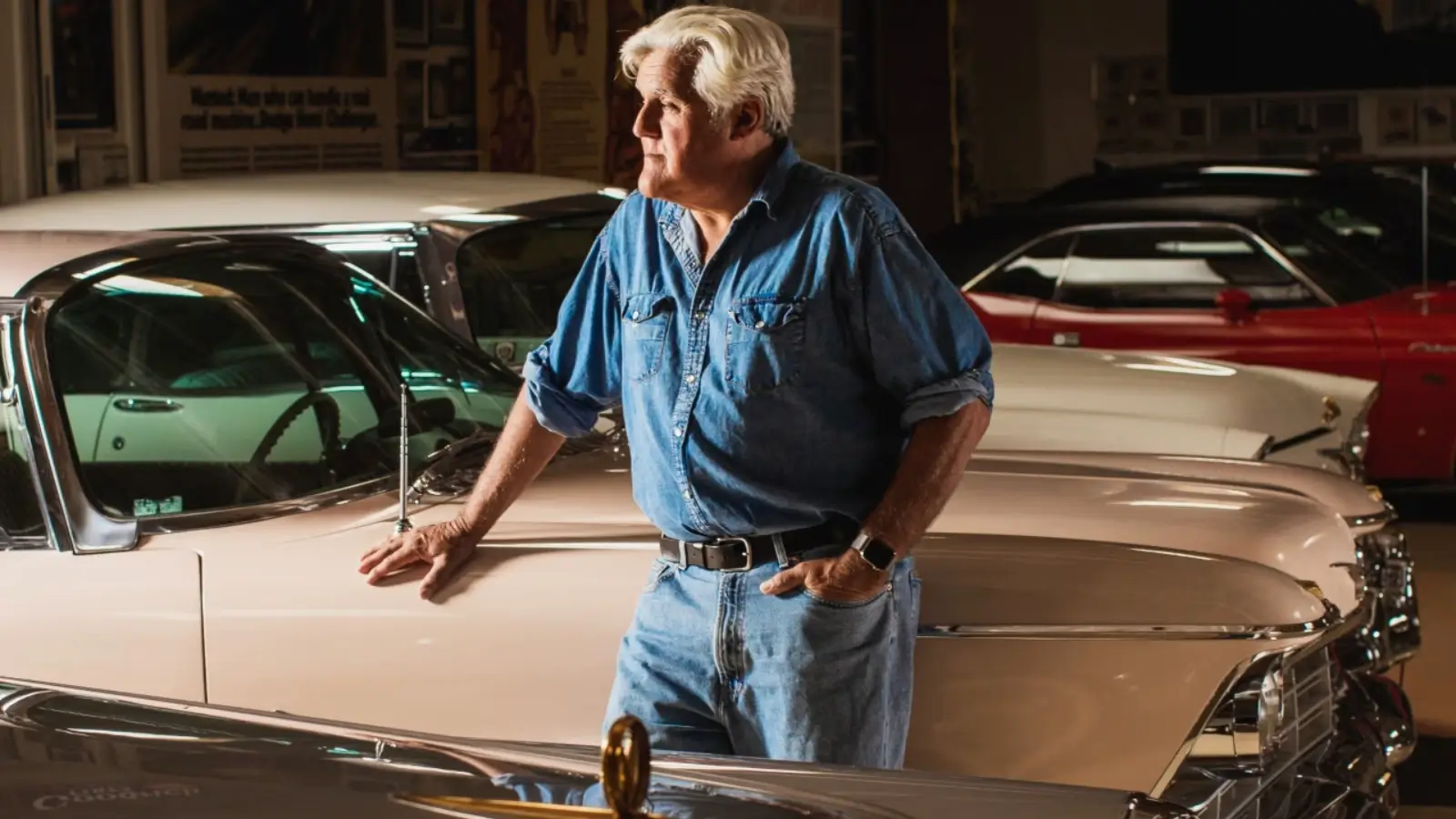

Small Tags, Big Job—Why Wire Labels Matter in Every Electronic Connection
Take a peek inside any modern device—whether it’s a sleek consumer gadget, a power-hungry server rack, or a sophisticated control system—and there’s one thing that consistently stands out amid the complexity: wires. Dozens, sometimes hundreds, of them, each carrying out a unique function. What keeps all of that circuitry from turning into chaos? A system that often goes unnoticed—wire labels.
These tiny tags might not get much spotlight, but they’re doing some of the heaviest lifting behind the scenes. From assembly lines to diagnostic benches, wire labels are essential for accuracy, safety, and speed. They don’t just keep things tidy. They make entire processes smarter, faster, and less prone to costly errors.
Electronics don’t speak for themselves. Without clear identifiers, figuring out which wire does what can quickly become a guessing game—one that’s frustrating at best and dangerous at worst. A single mix-up in polarity, signal, or grounding could result in a malfunction, a delayed rollout, or worse, a short circuit that fries an entire board.
That’s where wire labels come in. Each one acts like a name tag, making it immediately clear what that wire’s role is. When dealing with bundles of similar-looking cables in tight spaces, this clarity is crucial. It allows technicians, engineers, and quality control teams to work with speed and confidence instead of spending hours decoding cable paths manually.
And in electronics manufacturing, time really is money. Every second saved during testing, inspection, or installation has a direct impact on productivity and profit margins.
It’s not just about writing something down and sticking it on. In electronics, the label itself must be engineered for resilience. Heat, vibration, moisture, and tight bends are all part of the job. A paper label or low-grade adhesive won’t cut it.
That’s why specialized materials—like polyimide, vinyl, or heat-shrink tubing—are used to ensure longevity. These labels are designed to stick tight, resist fading, and stay readable even after years of exposure to heat from components or cleaning chemicals during service. Some even withstand reflow soldering environments or cryogenic freezing, depending on the industry.
And readability? That’s non-negotiable. If a barcode scanner can’t read the tag, or if text smears after installation, the label has already failed. That’s why durable printing methods—like thermal transfer—are often the standard for professional electronic labeling.
The journey of a wire label doesn’t end once a product is assembled. It continues to provide value long after it leaves the production line.
For field technicians, labels simplify maintenance and repairs. No need to dig through schematics just to figure out where a cable leads. The label says it all. That can be the difference between a 15-minute fix and a complete disassembly.
For customers, labeled wiring provides peace of mind. Whether it’s a smart home panel, industrial control system, or even a home theater setup, knowing each connection is clearly marked means troubleshooting becomes less of a headache. And for companies that handle large-scale installations, consistent wire labeling reinforces professionalism and trust in their brand.
Not every project uses the same wire, and not every wire gets the same label. In regulated industries—like aerospace, medical devices, or telecommunications—labeling isn’t just a best practice; it’s a requirement.
These sectors often demand compliance with strict labeling standards. That means labels must meet size, font, material, and adhesion guidelines. And when equipment is subject to audits or certifications, the wire labeling system can become a focal point.
Customization helps navigate these demands. Whether that means color-coded tags, serialized IDs, company logos, or multilanguage instructions, custom labeling supports both regulatory compliance and visual clarity.
Even in more flexible settings, tailored labeling improves workflow. Color matching, numbering sequences, or tags with built-in indicators (such as “HOT,” “GROUND,” or “TX”) all serve to make wiring systems easier to use and safer to manage.
Modern labeling isn’t just about ink and plastic. It’s about smart integration. With software-driven systems, manufacturers can automate label creation based on part numbers, CAD drawings, or bill-of-materials data. This means less manual input and fewer errors.
Labels with barcodes or QR codes link physical wiring to digital records. That way, a single scan can pull up the specs, origin, or history of a component. In large-scale manufacturing or data center environments, this kind of traceability makes asset management smoother and more scalable.
When the physical world of wiring meets the digital world of databases, that’s where efficiency skyrockets.
Skipping proper labeling might save a few minutes in the short term—but it can cost hours, or even days, later on. Mislabeled wires can delay production timelines, trigger product recalls, or create hazards for technicians. It’s not just an inconvenience—it’s a liability.
Rework, warranty claims, and brand damage are all risks that come with poor labeling practices. And in industries where precision is everything, even a small oversight can snowball into something much larger.
That’s why wire labels, despite their size, deserve serious attention. They’re not just an accessory to a job well done—they’re a fundamental part of it.
Every circuit begins with a connection. But every successful installation, repair, or upgrade begins with understanding those connections. That’s the real job of a wire label.
When clearly marked and built to last, these tags take the guesswork out of electronics. They keep systems safe, techs efficient, and products dependable. Whether tucked behind a panel or wrapped around a tiny internal wire, they’re doing quiet work that makes the whole system run smoother.
And in a world where technology is only getting more complex, that kind of reliability is more valuable than ever. So the next time there’s a need to clean up a wiring job, speed up production, or scale up quality, it might just start with something as small—and essential—as the right label.