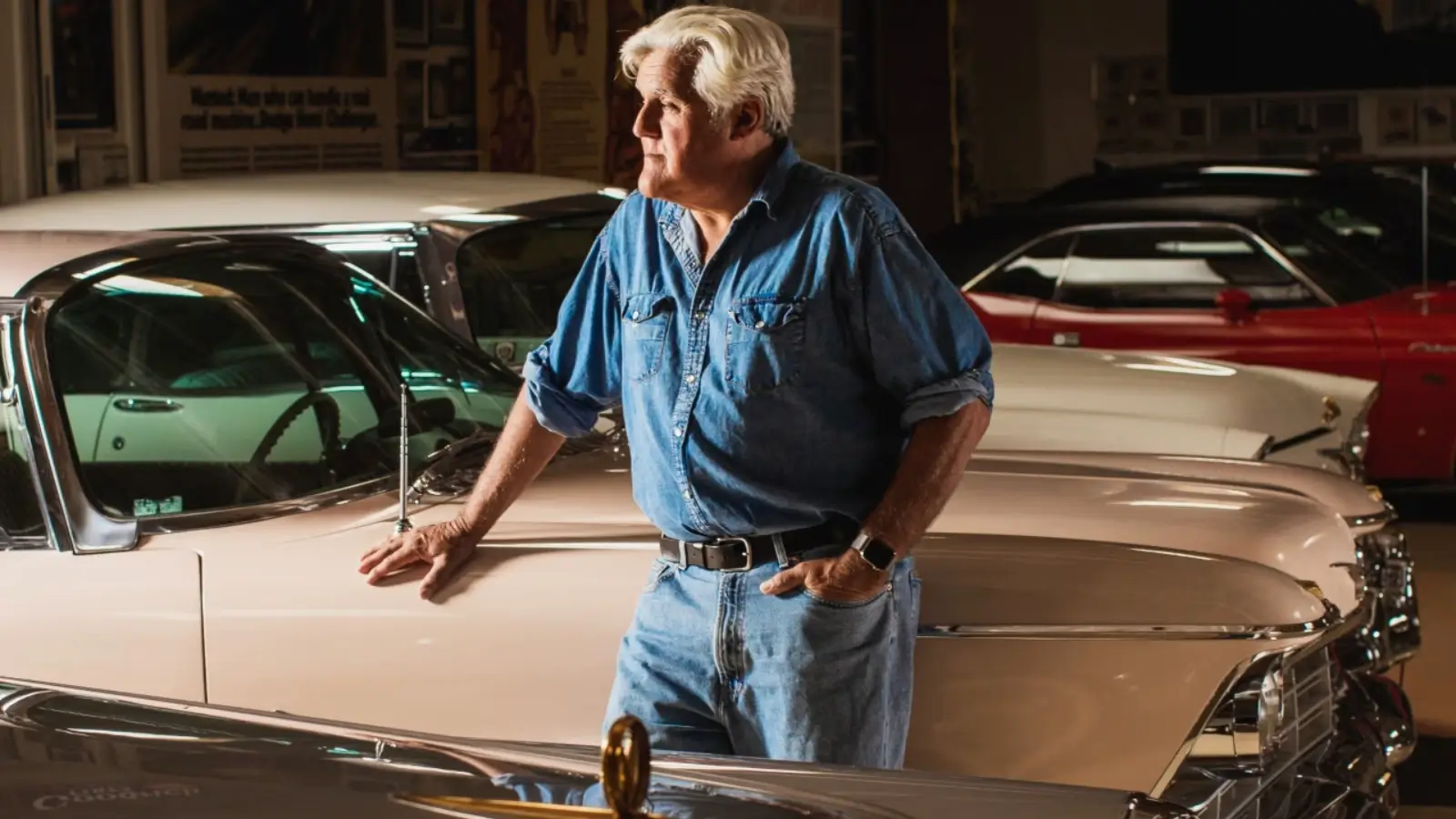

Precision isn’t just a goal when machining; it’s a necessity. Smart parameter selection (speed, feed rate, depth of cut, toolpath strategy, etc.) can mean the difference between a high-quality finished part and an expensive blunder. Sadly, it’s typical for machinists, mainly those new to CNC or manual machining, to make mistakes in parameter selection. Catch the signs early on to save time, tools, and materials.
Below are some of the more common symptoms that you might be using the wrong machining parameters:
If your completed piece has noticeable tool marks, harsh surfaces, or uneven finishes, it is usually a clue of incorrect feed rates or spindle speeds. If you run the tool too fast, you get chatter, and if it is too slow, rub instead of cut. But if the cut is too aggressive or the tool is brittle, then surface imperfections can also occur. Keep an eye on your finish quality—your machine might be trying to tell you something.
Too many tools needing frequent replacement or breaking unexpectedly is also an expensive red flag. Excessive tool wear can often be attributed to improper cutting parameters—speed, feed, and depth of cut. Running the spindle too fast can cause the tool to overheat while feeding too high can overload the tool. However, suppose your tooling does not last as long as it could. In that case, you may need to look into your machining parameters and review the tooling and material compatibility recommended by the manufacturer.
Chatter — a high-pitched, sometimes rhythmic vibration — is a sure sign that something’s wrong. It typically happens when there’s a misfit between machine stiffness, tool overhang, speed, and feed. Chatter not only diminishes surface quality but also leads to lasting damage to tooling and equipment. If you listen to it (and wouldn’t be alone), stop immediately and reset your parameters.
Are your components always out of specification? Poor dimensional accuracy—whether undersized holes, warped edges, or features not in alignment—can frequently be traced back to an incorrect combination of cutting parameters. Whether it is a tool flexing due to too much load, thermal expansion from titling the component due to too much heat from the spindle, or an unstable setup, the accuracy of your part is always at risk. This is especially important in low-tolerance sectors like aerospace or medical manufacturing.
You probably generate too much heat if you see discoloration or burning on the part or tool. This is often due to too high a speed or too slow a feed, which creates friction rather than cutting. Too much heat doesn’t just affect the workpiece—it can also damage the tool, shorten its lifespan, and alter material properties, all of which could compromise the integrity of the final product.
Scraping a workpiece against a tool generates a built-up edge (BUE), which changes the tool's geometry and affects its cutting ability. Incorrect speed and feed combinations or machining sticky materials such as aluminum without proper cooling or lubrication can cause broad banding. BUE can degrade tool performance, leading to a poor surface finish, dimensional inaccuracy, and premature failure of the tool.
If your machine reports spindle overload errors or the spindle load readings are higher than usual, it's running harder than it needs to. This could be a direct effect of erroneous parameters such as feed rate or depth of cut. Disregarding these indicators can cause mechanical wear or failure, so listen to those load readings!
Machining parameters are critical for optimal results in your operations. Regularly monitoring surface finish, tool wear, vibration, and heat can warn you of problems before they become critical. If you encounter any of the signs referenced above, refer to your tool manufacturer’s recommendations, review material machining charts/percent stock removal, and possibly conduct a test cut before ramping to full production.
Everything is a detail in machining. So getting your parameters right saves you time and money — it leads to smoother, more efficient workflow and higher quality end products.