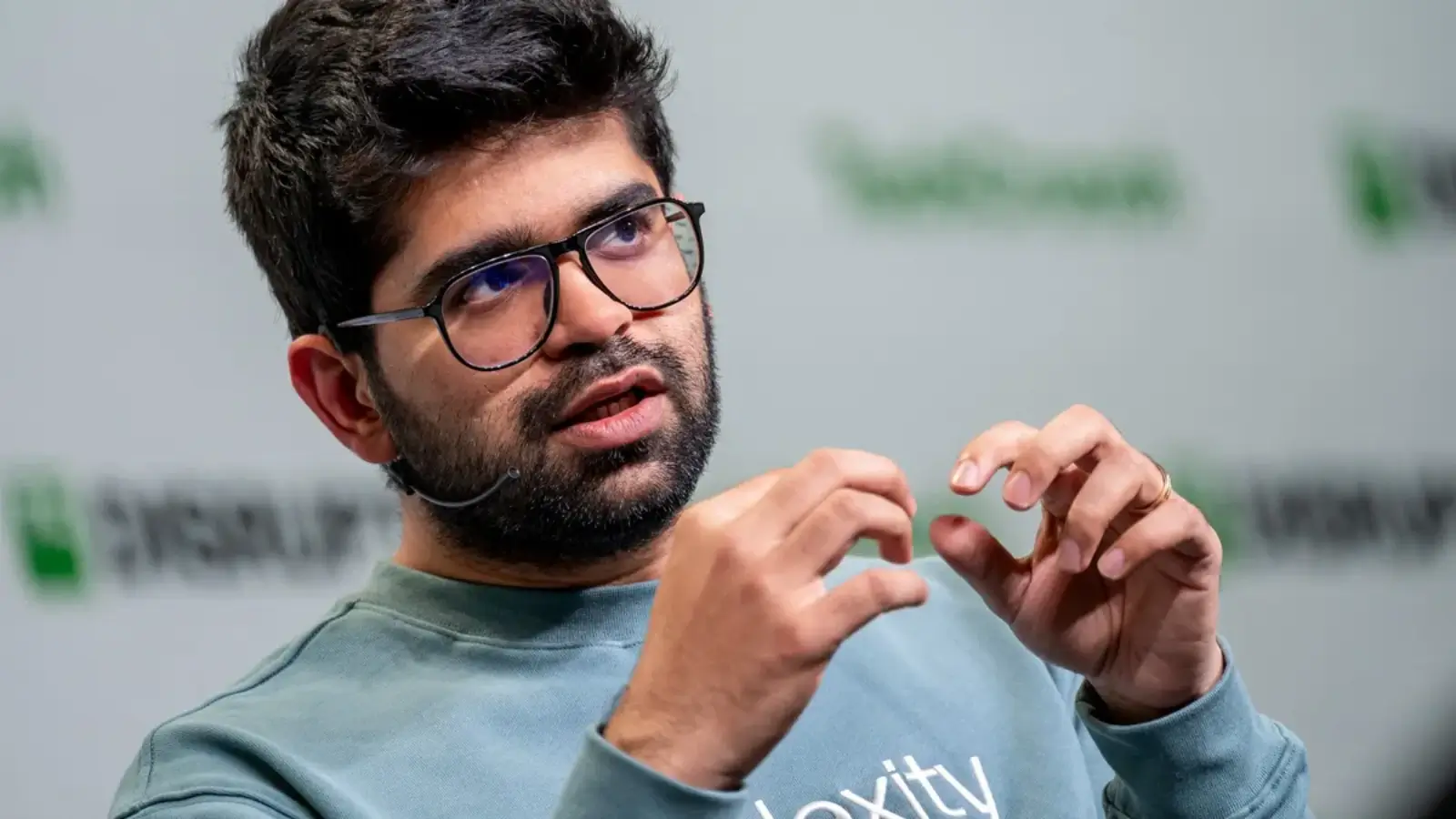

Workplaces today are undergoing a paradigm shift in the way they tend to employee wellness. Those days of merely equipping the workplace with hard hats and goggles are over. Today's progressive companies understand that real employee care goes beyond mere protection to include the avoidance of long-term injury and easing daily physical stress.
This transformation is most clearly seen in packaging and logistics settings, where repetitive processes have long caused harm to workers' bodies. But the future is changing this, as smart automation brings solutions that not only safeguard employees but also increase operational efficiency.
In warehouses and packaging plants worldwide, employees execute thousands of repetitive movements every day. From carrying boxes to taping things down, these apparently mundane activities add up to substantial physical strain in the long run. The data paint a disturbing picture: repetitive strain injuries (RSIs) account for about 30% of total workplace injury, and workers in the packaging and logistics industries are particularly at risk.
Manual packaging operations commonly involve workers to be in awkward positions, doing fast hand movements, and exerting force repeatedly during their shifts. All these activities contribute to the development of conditions like carpal tunnel syndrome, tendonitis, and chronic back pain. Besides the human cost, the injuries contribute to more workers' compensation claims, higher turnover, and lower productivity.
The classic strategy of just rotating employees between tasks or giving them ergonomic training, while useful, does not deal with the underlying issue. The fix is to rethink how things are accomplished through smart automation.
Smart automation technology is transforming workplace safety by assuming responsibility for the most physically taxing and repetitive parts of industrial labor. Instead of replacing employees, these technologies act as strong partners that bear the burden while workers concentrate on more valuable work that demands human insight and imagination.
The secret to effective workplace automation is finding very specific pain points and addressing them with very specific solutions. For packaging operations, that usually entails fixing the repetitive motion of sealing, labeling, and preparing shipments.
Perhaps the most significant development in this area is the carton sealing machine. This innovation solves one of the most prevalent causes of repetitive strain in packaging plants: continuously using tape to close boxes.
Old-fashioned manual taping makes workers extend their arms hundreds of times, exert downward pressure, and make cutting motions repeatedly during a shift. It is these multiple arm reaches, pressures, and cuts that provide the optimal situation to develop RSIs in the shoulders, wrists, and forearms.
Carton sealing machines cut back on these same motions by automatically applying tape to boxes as they travel through the machine. Employees merely need to feed boxes into place, and the machine executes the controlled application of tape with consistent pressure and cutting. This automation prevents the potential for injury and still guarantees every package receives professional-quality sealing.
The ergonomic advantages go beyond just reducing repetitive movement. These machines can be operated at a comfortable level, so laborers are not constantly required to bend or reach in uncomfortable ways. The steady operation also allows workers to have more stamina throughout the day, with less overall strain on their bodies.
While injury prevention is the primary driver for adopting automation tools, the benefits extend far beyond safety metrics. Companies implementing these solutions report significant improvements across multiple operational areas.
Enhanced Productivity: Automated sealing systems can process packages significantly faster than manual methods, often doubling or tripling throughput. This increased efficiency allows companies to handle higher volumes without requiring additional staff or extended hours.
Better Quality Control: Human fatigue causes uneven tape application, which can cause packages to open while in transit. Automatic systems apply tape with consistent pressure and coverage each time, cutting shipping damage and customer complaints.
Improved Employee Happiness: When employees are relieved of the most physically challenging duties, they indicate greater job satisfaction and are more likely to remain with the business in the long term. This decreased turnover saves substantial amounts of money on the recruitment and training of new staff.
Scalability: As volumes of business change, computerized systems can readily adjust to manage fluctuating workloads without the necessity for short-term hiring or requiring current staff to work overtime.
Training is essential for achieving the full potential of automation tools. Employees must learn how to use new devices safely and effectively. Instruction should involve not only technical use but also the ergonomic design principles of the tools.
Regular monitoring and feedback gathering assist with ensuring that automation solutions remain aligned with their intended purpose. Firms need to monitor both safety levels and worker satisfaction to assess the actual effectiveness of their investments.
As technology keeps developing, the potential for automating aid to workers will only grow. Artificial intelligence, smart sensors, and robotics are paving the way for eliminating physical strain and enhancing workplace safety.
Those firms that understand automation as a means of empowering employees, not replacing them, will be best equipped to attract and retain the best people and keep operations competitive. By investing in solutions that keep workers' best interests at heart, firms create settings where both people and profits can flourish.
Industrial workplace transformation with careful automation is more than technological progress—it's an inherent move toward realizing the value of human potential and safeguarding those who make businesses thrive.